UMass Amherst researchers leading project to advance scalable manufacturing innovations for high-efficiency/low-cost metalenses
Project aims to demonstrate full-scale optical wafer processing for next-generation smartphone cameras, medical imaging devices, and more
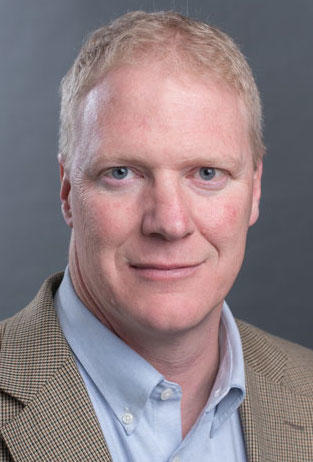
AMHERST, MA. – Researchers at the University of Massachusetts Amherst are leading an initiative to advance scalable manufacturing processes that enable commercial fabrication of highly refractive metalenses, which could allow these high-performing optical wafers to be widely used in next-generation smartphone cameras, medical imaging devices, and more.
Metalenses manipulate light and eliminate chromatic aberrations. Unlike classical refractive lenses which are curved and often bulky, metalenses are flat and wafer-thin. Efficient metalenses rely on subwavelength elements with precise shape, small pitch, and critical dimensions below 100 nanometers. Until now, prototype lenses at this dimension have only been fabricated using multi-step subtractive processing technologies and traditional semiconductor equipment. Because yields through this specialized process can be low, production costs are high.
Innovation in the space is relentless, driven by the need to miniaturize optics that enable diverse products - from augmented and mixed reality glasses that are feature-rich, yet ultra-light and stylish - to camera lenses and sensors on smartphones that improve image capture and can be embedded in the back case. The World Economic Forum has identified metalenses as a top-10 emerging technology with the potential to “positively disrupt the existing order.”
Leading the “Research Partnership for Scalable Metalens Fabrication” project is polymer science and engineering professor James Watkins, director of UMass Amherst’s Center for Hierarchical Manufacturing (CHM). Co-principal investigator is metasurface design expert Amir Arbabi, UMass Amherst assistant professor of electrical and computer engineering. They aim to show that high-efficiency metalenses with refractive indices as high as 2.10 can be fabricated at commercial scale using efficient nanoimprint processes designed by the CHM team.
“For the past couple of years my team has been working on the design and fabrication of high-performance, all inorganic metalenses using an innovative, commercializable, and cost-effective additive manufacturing approach,” says Watkins. “We believe this approach will enable our partners to be first to market with a superior product that cannot otherwise be manufactured in a scalable manner.”
Teaming with Watkins and Arbabi are materials partner Pixelligent, which is supplying its ultrahigh refractive index PixClear® titania nanomaterials, and nano-optical and x-ray components manufacturer MOXTEK.
The project is supported by a grant from the National Science Foundation. Promising results by the UMass team were recently published in the journal ACS Photonics.